2025 Pengarang: Howard Calhoun | [email protected]. Terakhir diubah: 2025-01-24 13:18
Pengecoran dalam cetakan cangkang juga disebut pengecoran cangkang. Dan di luar negeri, cara kerja ini disebut Shell.
Informasi umum
Dalam industri industri saat ini, banyak metode pengecoran yang berbeda digunakan. Selain casting shell, casting investasi juga digunakan, serta dalam cetakan logam dan beberapa metode lainnya. Keuntungan keseluruhan dari metode pengecoran ini, jika dibandingkan dengan cetakan pasir, adalah bahwa mereka menghasilkan bahan akhir yang lebih akurat dalam hal bentuk dan dimensi. Selain itu, jumlah kekasaran pada permukaan produk tersebut berkurang. Dalam kasus yang lebih jarang, tetapi masih terjadi bahwa kebutuhan untuk pemesinan berikutnya setelah peleburan dihilangkan. Selain segalanya, penggunaan pengecoran dalam cetakan cangkang dan metode lain berkontribusi pada fakta bahwa proses ini dapat dimekanisasi sebanyak mungkin, akibatnya otomatisasinya juga meningkat. Dan ini, tentu saja, sangat meningkatkan produktivitas fasilitas industri mana pun.
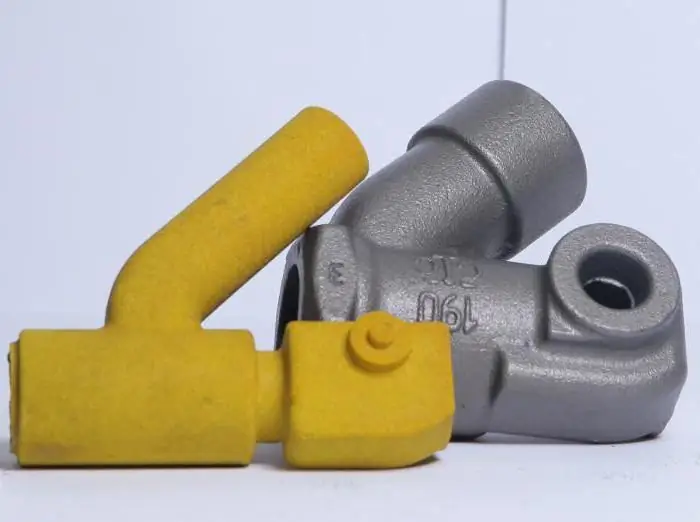
Pengecoran cangkang
Jika kita berbicara secara khusus tentang iniMetode ini pertama kali diperkenalkan di pabrik pada tahun 1953. Saat ini, metode tersebut digunakan cukup luas. Pengecoran dalam cetakan cangkang, misalnya, yang memproduksi sebagian besar suku cadang untuk traktor Kirovets. Semua bagian yang diproduksi menggunakan metode ini memiliki kualitas terbaik dari baja atau besi tuang. Pengecoran cangkang adalah suatu metode dimana hasil akhir pengecoran memiliki bentuk yang terdiri dari dua cangkang pasir-resin. Juga, metode pembuatan suku cadang ini hanya digunakan dalam kasus-kasus di mana perlu untuk membuat suku cadang dengan dimensi kecil atau sedang, tetapi pada saat yang sama dengan akurasi tinggi. Contoh penerapan metode pengecoran ini adalah suku cadang mesin atau pengecoran dinding tipis.
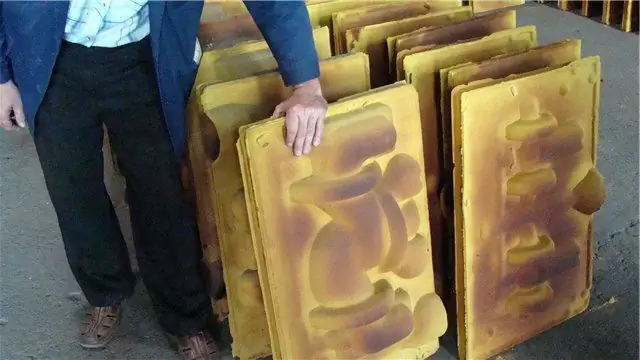
Inti dari Jalan
Dengan metode kerja ini, Anda bisa mendapatkan berbagai suku cadang untuk kipas, motor, pompa, atau mesin tekstil. Namun, panjang maksimum produk yang diterima tidak boleh melebihi 1 meter, dan beratnya tidak boleh lebih dari 200 kg.
Inti dari pengecoran ke dalam cetakan cangkang didasarkan pada sifat-sifat tertentu dari resin termoset, yang merupakan bagian dari campuran pasir-resin. Keuntungan menggunakan komponen tersebut adalah resin ini cenderung cepat dan permanen mengeras bila dirawat dengan suhu 200-250 derajat Celcius.
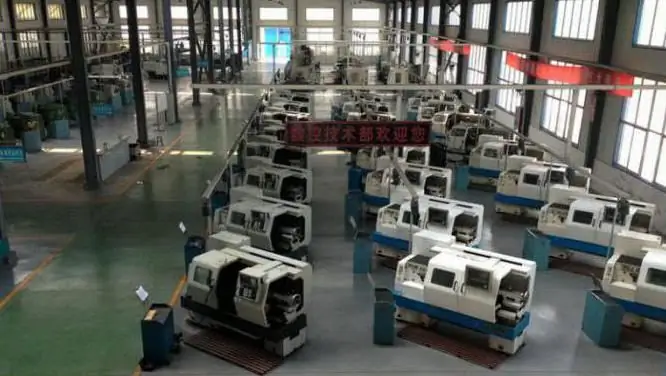
Membuat cetakan cangkang untuk casting
Untuk membuat cetakan untuk pengecoran berikutnya, perlu memiliki pasir kuarsa berbutir halus, yang dilengkapi dengan penambahan resin termoset, yang merupakan elemen penghubungnya untuk mendapatkan cetakan cangkang yang lengkap. Bahan-bahan ini, khususnya resin, dipilih karena mengeras ketika melewati penghalang suhu tertentu. Proses pembuatannya adalah sebagai berikut. Pertama, resin dipanaskan hingga 140-160 derajat Celcius. Di bawah pengaruh lingkungan seperti itu, ia berubah menjadi massa perekat cair yang sepenuhnya menyelimuti cetakan pasir kuarsa.
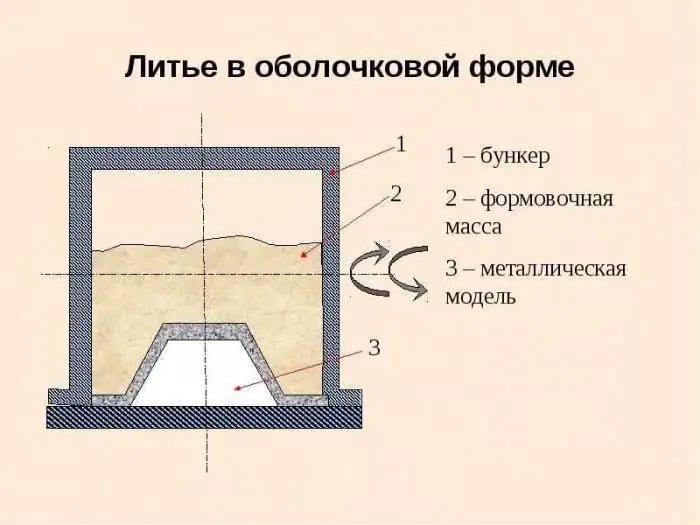
Cakupan pengecoran dalam cetakan cangkang cukup luas, oleh karena itu proses pembuatan cetakan dibawa ke otomatis atau otomatis.
Setelah cetakan benar-benar tertutup resin, suhu dinaikkan menjadi 200-250 derajat Celcius. Ambang suhu ini cukup untuk massa perekat mengeras dan membentuk suatu bentuk. Selanjutnya, ketika proses pengecoran bagian dimulai, yaitu ketika logam cair memasuki cetakan, suhu di dalamnya mencapai sekitar 600 derajat. Mode ini cukup untuk memastikan bahwa resin tidak meleleh, tetapi terbakar, sementara meninggalkan pori-pori pada cetakan itu sendiri, memfasilitasi keluarnya gas.
Keuntungan dan kerugian dari pengecoran cetakan shell
Seperti proses manufaktur lainnya, proses ini memiliki pro dan kontra. Jika kita membandingkan metode casting ini, misalnya, dengan casting incetakan pasir biasa, ada beberapa keunggulan:
- Perbedaan pertama dan agak signifikan adalah kelas akurasi, yaitu 7-9. Selain itu, permukaan akhir dari bagian yang diperoleh ditingkatkan hingga 3-6. Selain itu, kelonggaran dikurangi, yang diperbolehkan untuk pemesinan berikutnya dari bagian yang dihasilkan setelah pengecoran.
- Salah satu keuntungan besar adalah pengurangan yang signifikan dalam biaya tenaga kerja untuk pembuatan coran.
- Metode pengecoran ini mengurangi konsumsi bahan cetakan, serta jumlah logam karena ukuran saluran gerbang berkurang.
- Mengurangi jumlah pernikahan secara signifikan.
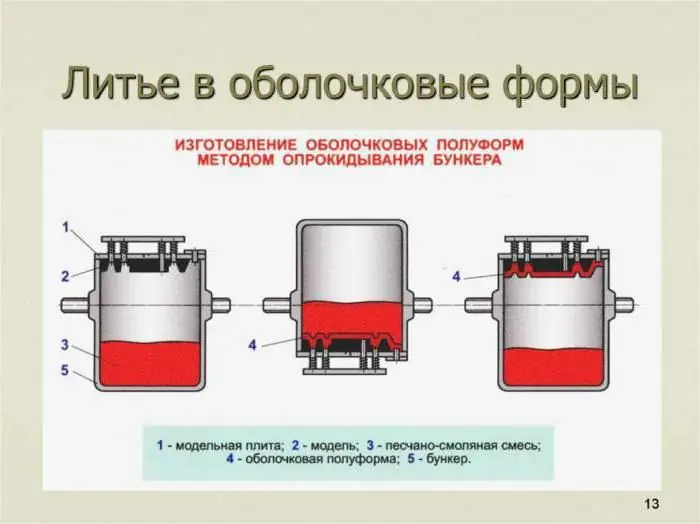
Namun, ada beberapa kelemahan pengecoran dalam cetakan cangkang. Ini termasuk:
- Kehidupan cetakan cangkang - 1 pengecoran.
- Biaya pencetakan pasir cukup tinggi.
- Persentase gas berbahaya yang tinggi.
Proses pembentukan korpus
Proses pembentukan tubuh dilakukan dalam enam tahap:
- Langkah pertama adalah proses menuangkan campuran ke model logam panas, serta proses menyimpannya selama beberapa puluh detik hingga terbentuk kerak tipis dan kuat di sekitar bagian. Paling sering, model terbuat dari besi cor, dan pemanasannya dilakukan hingga 230-315 derajat.
- Setelah itu, perlu dilakukan operasi untuk menghilangkan pasir cetakan berlebih. Ketebalan kerak pada akhirnya harus dari 10 hingga 20mm. Itu tergantung pada waktu tinggal campuran pada model, serta pada suhu.
- Setelah itu, perlu untuk memindahkan pelat model bersama dengan cetakan ke oven, di mana mereka akan berada sampai akhir proses pengawetan. Pada akhir prosedur ini, kekuatan cangkang harus antara 2,4 dan 3,1 MPa.
- Setelah dikeluarkan dari tungku, cangkang yang mengeras dipindahkan dari pelat. Sebuah pendorong khusus digunakan untuk prosedur ini.
- Setelah itu, dua atau lebih model diikat menjadi satu menggunakan semacam penjepit atau dengan cara direkatkan. Cetakan ini dapat digunakan untuk pengecoran dalam cetakan cangkang atau hanya disimpan. Umur simpan hampir tidak terbatas.
- Sebelum memulai proses pengecoran dalam cetakan yang sudah jadi, tembakan dituangkan ke dalamnya, yang membantu mencegah atau menghancurkan cetakan selama penuangan lebih lanjut.
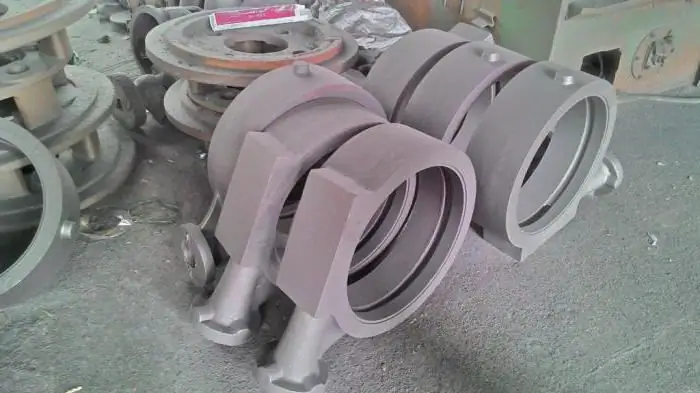
Detail Casting
Perlu dimulai dengan fakta bahwa toleransi tipikal yang diizinkan dalam pembuatan perkakas bisa 0,5 mm. Kekasaran permukaan diperbolehkan dalam kisaran 0,3 hingga 0,4 mikron. Batas seperti itu dibenarkan oleh fakta bahwa pasir berbutir halus digunakan. Juga perlu diperhatikan: penggunaan resin sangat berkontribusi pada fakta bahwa permukaannya sangat halus.
Volume produksi
Untuk terlibat dalam produksi cetakan dan suku cadang seperti itu, perlu diperhatikan pemasangan model cetakan. Waktu yang dibutuhkan untuk pemasangan kurang dari seminggu. Setelah instalasi selesai, jumlah output dapatmencapai 5 hingga 50 buah per jam. Volume produksi per jam seperti itu cukup nyata, namun untuk ini perlu mempersiapkan proses pengecoran yang sesuai. Bahan utama yang akan dibutuhkan untuk pengecoran adalah besi tuang, aluminium, tembaga, serta paduan dari jenis logam ini. Bahan lain yang diperlukan adalah paduan yang menggunakan aluminium dan magnesium.
Direkomendasikan:
Pengecoran baja berkelanjutan: prinsip operasi, peralatan yang diperlukan, kelebihan dan kekurangan metode ini
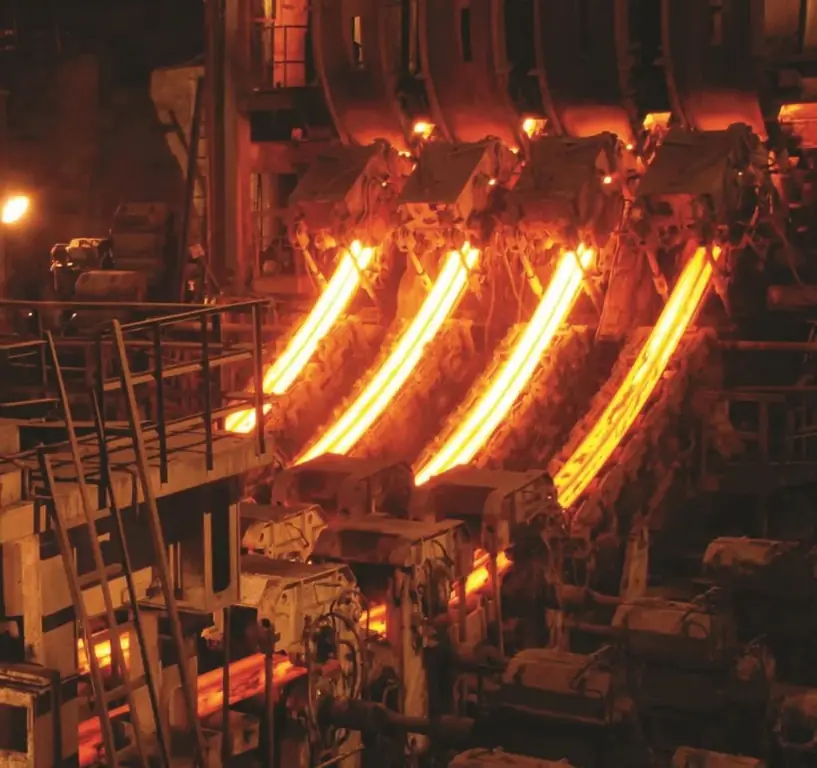
Saat ini, berbagai macam barang, suku cadang, dll. terbuat dari baja. Tentu saja, ini membutuhkan bahan sumber dalam jumlah besar. Oleh karena itu, pabrik telah lama menggunakan metode pengecoran baja kontinu, yang dicirikan oleh fitur terpenting - produktivitas tinggi
Lokomotif listrik 2ES6: sejarah pembuatan, deskripsi dengan foto, karakteristik utama, prinsip operasi, fitur operasi dan perbaikan
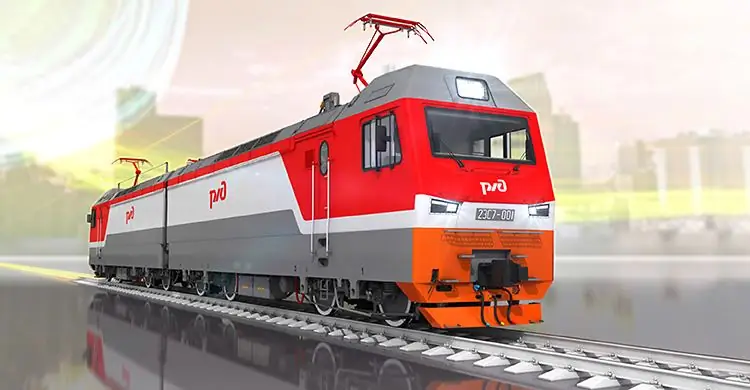
Saat ini, komunikasi antar kota, transportasi penumpang, pengiriman barang dilakukan dengan berbagai cara. Salah satunya adalah jalur kereta api. Lokomotif listrik 2ES6 merupakan salah satu jenis transportasi yang saat ini aktif digunakan
Casting dalam cetakan silikon: peralatan. Pengecoran vakum dalam cetakan silikon
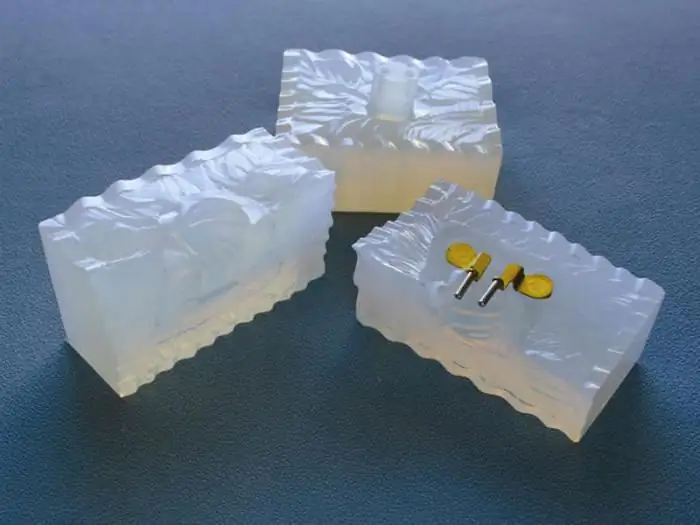
Untuk pembuatan sejumlah kecil plastik kosong, pengecoran vakum ke dalam cetakan silikon paling sering digunakan. Cara ini cukup ekonomis (membuat cetakan logam membutuhkan lebih banyak waktu dan biaya). Selain itu, cetakan silikon digunakan berulang kali, dan ini juga secara signifikan mengurangi biaya produksi
Dasar psikofisiologis dari aktivitas pengemudi. Dasar-dasar psikofisiologi tenaga kerja pengemudi
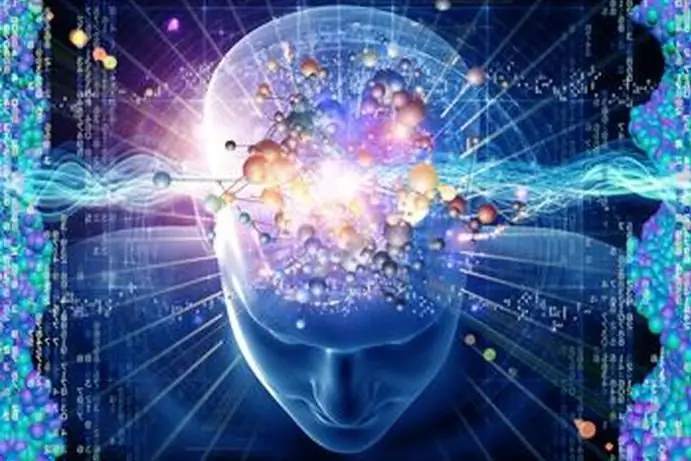
Datang ke kursus mengemudi, tidak setiap orang siap dengan kenyataan bahwa, selain mempelajari aturan perilaku di jalan, ia harus mempelajari dasar-dasar psikofisiologis dari aktivitas pengemudi. Namun pertanyaan-pertanyaan ini tidak kalah pentingnya dengan keterampilan memiliki mobil
Sistem gerbang: jenis, perangkat. pengecoran cetakan
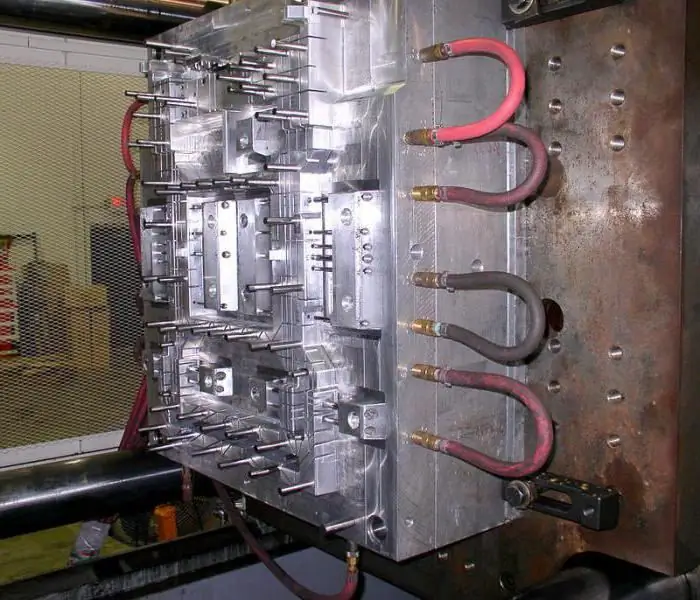
Sistem gerbang: prinsip operasi, deskripsi, fitur, perangkat, operasi. Cetakan untuk casting: tujuan, karakteristik, foto