2025 Pengarang: Howard Calhoun | [email protected]. Terakhir diubah: 2025-01-24 13:18
Saat ini, berbagai macam barang, suku cadang, dll. terbuat dari baja. Tentu saja, ini membutuhkan bahan sumber dalam jumlah besar. Oleh karena itu, pabrik telah lama menggunakan metode pengecoran baja kontinu, yang dicirikan oleh fitur terpenting - produktivitas tinggi.
Peralatan penting untuk bekerja
Sampai saat ini, beberapa instalasi untuk pengecoran baja dengan cara ini dikenal, dan disingkat UNRS. Awalnya, instalasi tipe vertikal dikembangkan dan mulai diproduksi, terletak 20-30 meter di bawah permukaan lantai bengkel. Namun, kemudian keinginan untuk meninggalkan pendalaman lantai menjadi mesin utama untuk pengembangan instalasi ini. Hal ini menyebabkan pengembangan dan implementasi pabrik pengecoran kontinyu tipe menara. Ketinggian instalasi ini adalah 40 m, namun versi mesin ini tidak banyak digunakan karena dua alasan. Pertama, membangununit seperti itu di bengkel cukup bermasalah dan melelahkan. Kedua, lebih banyak kesulitan muncul dengan operasinya.
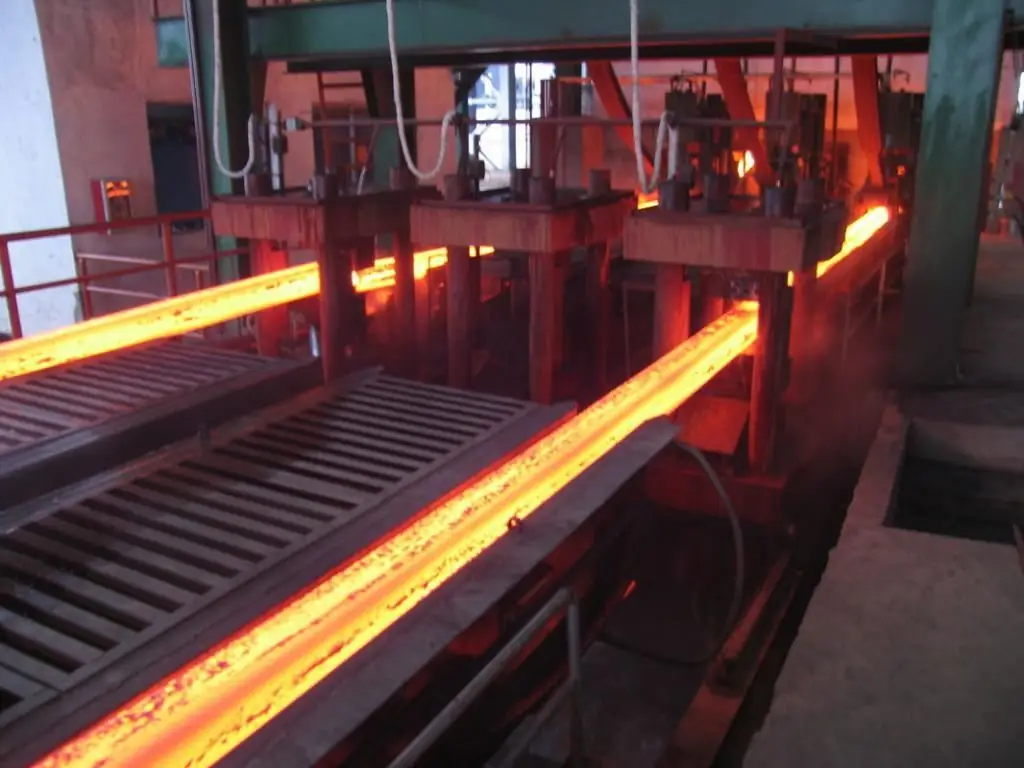
Instalasi melengkung dan radial
Seiring waktu, pengecoran baja terus-menerus dialihkan untuk bekerja dengan mesin pembengkok vertikal. Fitur utama adalah pembengkokan ingot yang keluar setelah poros sebesar 90 derajat. Setelah itu, mekanisme pelurusan khusus digunakan dalam pemasangan untuk meluruskan ingot, dan baru setelah tahap ini pemotongan dilakukan. Pengecoran baja secara terus-menerus pada peralatan semacam itu tidak menjadi sangat populer karena beberapa alasan. Pertama, tikungan, tentu saja, memungkinkan untuk mengurangi ketinggian, tetapi pada saat yang sama sangat membatasi penampang batang itu sendiri. Semakin banyak yang diperlukan untuk mendapatkan bagian material, semakin besar tikungan yang harus dibuat, yang berarti ketinggiannya meningkat lagi. Kedua, mesin bending ditempatkan di toko baja dengan kesulitan yang lebih besar daripada yang vertikal.
Saat ini, instalasi untuk pengecoran kontinyu baja radial semakin populer. Pada unit seperti itu, ingot dibentuk dalam cetakan dan meninggalkannya di sepanjang busur yang sama di mana ia memasukinya. Setelah itu, akan diluruskan dengan mekanisme pull-correct. Dan kemudian Anda sudah bisa mulai memotong ingot menjadi kosong. Desain inilah yang dalam praktiknya ternyata paling rasional dalam mengatur arus barang di toko baja.
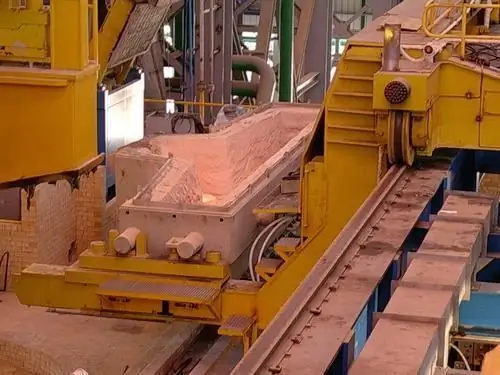
Di mana casting dimulai
Teknologi berkelanjutanpengecoran baja adalah proses yang agak rumit. Namun, adil untuk mengatakan bahwa prinsipnya tetap sama terlepas dari pengaturan produksi yang digunakan. Anda dapat mempertimbangkan teknologi menggunakan contoh UNRS vertikal.
Mesin ini dilengkapi dengan sendok untuk menuangkan baja melalui derek khusus. Setelah itu, baja mengalir ke tundish, yang memiliki sumbat. Untuk mesin single strand akan ada satu stopper, untuk mesin multi strand akan ada satu stopper per aliran. Selain itu, tundish memiliki baffle khusus untuk menahan terak. Dari tundish, baja akan mengalir ke dalam cetakan, melewati gelas takar atau sumbat. Penting untuk dicatat di sini bahwa sebelum pengecoran pertama, benih dimasukkan ke dalam cetakan dari sisi bawah. Ini mengisi baik penampang seluruh cetakan, atau hanya bentuk benda kerja. Lapisan atas benih akan menjadi bagian bawah cetakan. Selain itu, ia juga memiliki bentuk ekor burung walet untuk memasang ingot di masa depan.
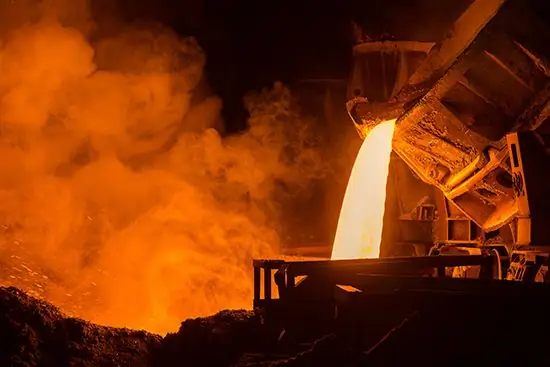
Casting lebih lanjut
Selanjutnya, dalam proses pengecoran baja terus menerus, perlu menunggu sampai tingkat bahan baku naik di atas benih hingga ketinggian sekitar 300-400 mm. Ketika ini terjadi, mekanisme dimulai, yang membawa perangkat penarik ke dalam operasi. Ini memiliki gulungan tarik, di bawah pengaruh benih yang akan jatuh dan menarik ingot yang dibuat bersamanya.
Mesin continuous casting memiliki cetakan yang biasanya terbuat dari tembaga dengan dinding berlubang. Dia berada di bawah intensoleh aksi air pendingin, dan bagian dalamnya sesuai dengan bentuk batangan yang akan diperoleh. Di sinilah kerak kosong ingot terbentuk. Pada kecepatan pengecoran tinggi, robekan kerak ini dan kebocoran logam dapat terjadi. Untuk menghindari hal ini, cetakan ditandai dengan gerakan bolak-balik.
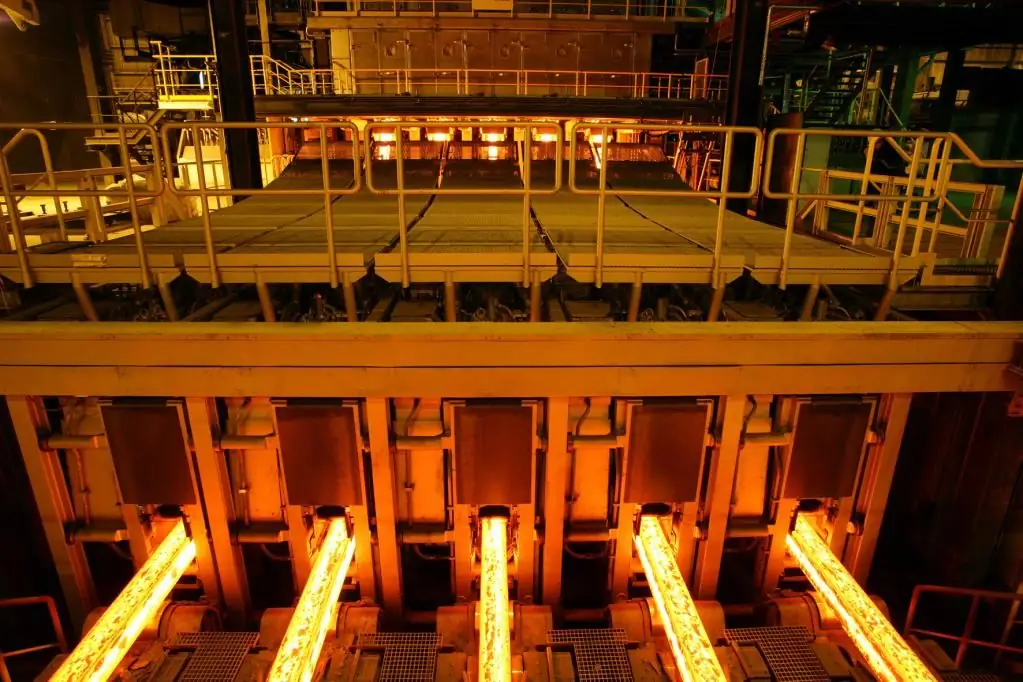
Karakteristik operasi cetakan
Mesin continuous casting memiliki motor listrik yang bertanggung jawab untuk menciptakan gerakan bolak-balik ini. Ini dilakukan melalui kekuatan gearbox dengan mekanisme ayun tipe cam. Pertama, cetakan bergerak ke arah yang sama dengan benda kerja, yaitu ke bawah, dan setelah proses selesai, ia kembali ke atas. Langkah ayunan adalah dari 10 hingga 40 mm. Cetakan adalah kompartemen penting dalam pengecoran baja terus menerus pada semua jenis peralatan, dan oleh karena itu dindingnya dilumasi dengan parafin atau pelumas lain yang sesuai dengan karakteristiknya.
Perlu dicatat bahwa pada peralatan modern tingkat logam dikontrol secara radiometrik dengan menerapkan sinyal kontrol ke penghenti sendok. Dalam cetakan itu sendiri, atmosfer netral atau pereduksi dapat dibuat di atas level logam untuk menghindari oksidasi produk selama produksi.
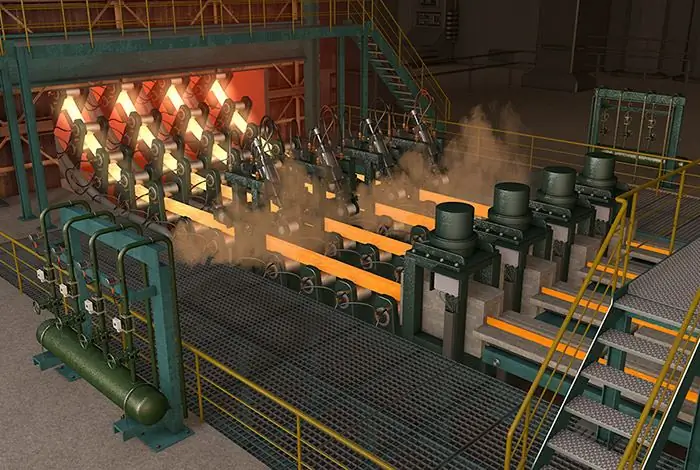
Kulit batang ingot
Perlu dicatat bahwa bekerja di bawah vakum juga dianggap sebagai metode pengecoran yang menjanjikan. Satu unit dapat melakukanmenuangkan melalui beberapa cetakan sekaligus. Dengan demikian, jumlah aliran satu instalasi dapat mencapai hingga delapan.
Aksi heat sink dari cold seed digunakan untuk membentuk bagian bawah kulit batangan. Ingot akan keluar dari cetakan di bawah pengaruh benih, yang ditarik ke zona pendinginan sekunder (SCZ). Di tengah billet, baja akan tetap dalam keadaan cair. Penting untuk dicatat di sini bahwa, sesuai dengan persyaratan teknologi pengecoran baja, ketebalan kulit harus minimal 25 mm pada saat keluar dari cetakan. Untuk memenuhi persyaratan ini, perlu untuk memilih laju aliran material yang tepat.
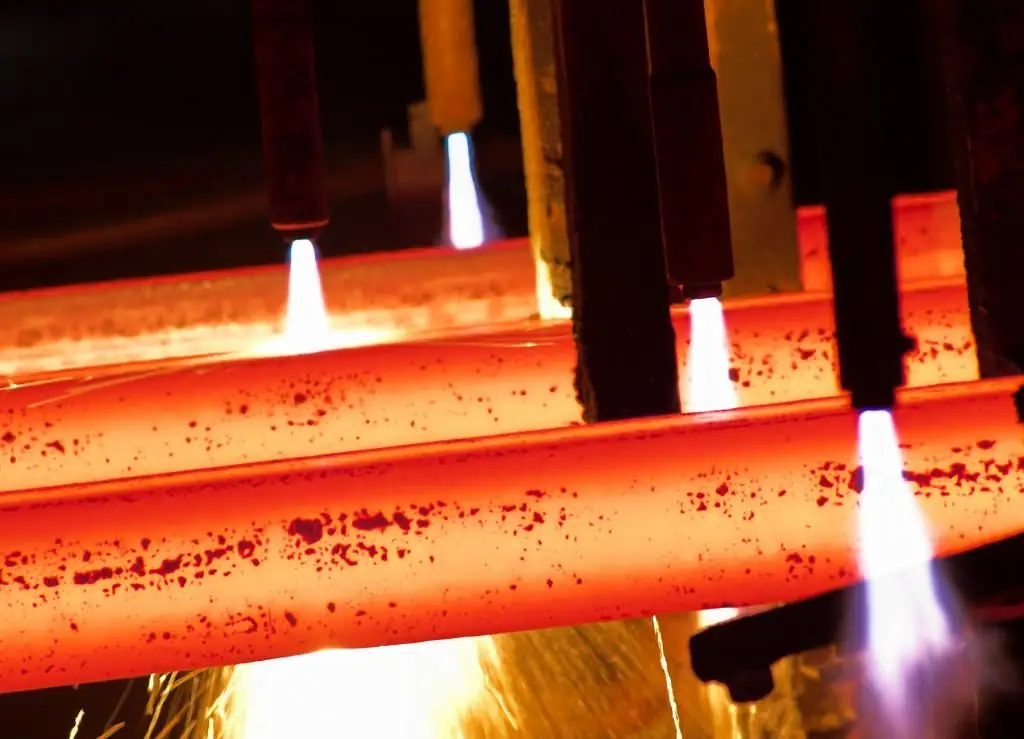
Karakteristik proses instalasi dan casting
Karakteristik teknologi kira-kira sebagai berikut. Jika bagian ingot adalah 160x900 mm, maka kecepatannya harus dari 0,6 hingga 0,9 m/mnt. Jika penampangnya 180x1000 mm, maka kecepatannya dikurangi menjadi 0,55-0,85 m/menit. Indikator kecepatan tertinggi diperlukan untuk penampang ingot tipe persegi 200x200 mm - 0,8-1,2 m/mnt.
Berdasarkan indikator di atas, kita dapat menyimpulkan bahwa kecepatan rata-rata casting satu untai menggunakan teknologi continuous casting adalah 44,2 t/jam. Jika Anda melebihi kecepatan optimal, porositas pusat akan meningkat.
Selanjutnya, perlu dicatat bahwa stabilitas pengecoran dan kualitas produk itu sendiri dipengaruhi oleh suhu logam. Secara empiris, ditemukan bahwa pada suhu lebih dari 1560 derajatCelcius permukaan ingot sering tertutup retakan. Jika suhu lebih rendah dari yang ditunjukkan, maka kaca akan sering dikencangkan. Dengan demikian, ditemukan bahwa suhu optimal untuk metode pengecoran baja kontinyu adalah 1540-1560 derajat Celcius. Untuk mempertahankan indikator ini, suhu pemanasan tungku sebelum pelepasan harus berada di kisaran 1630-1650 derajat.
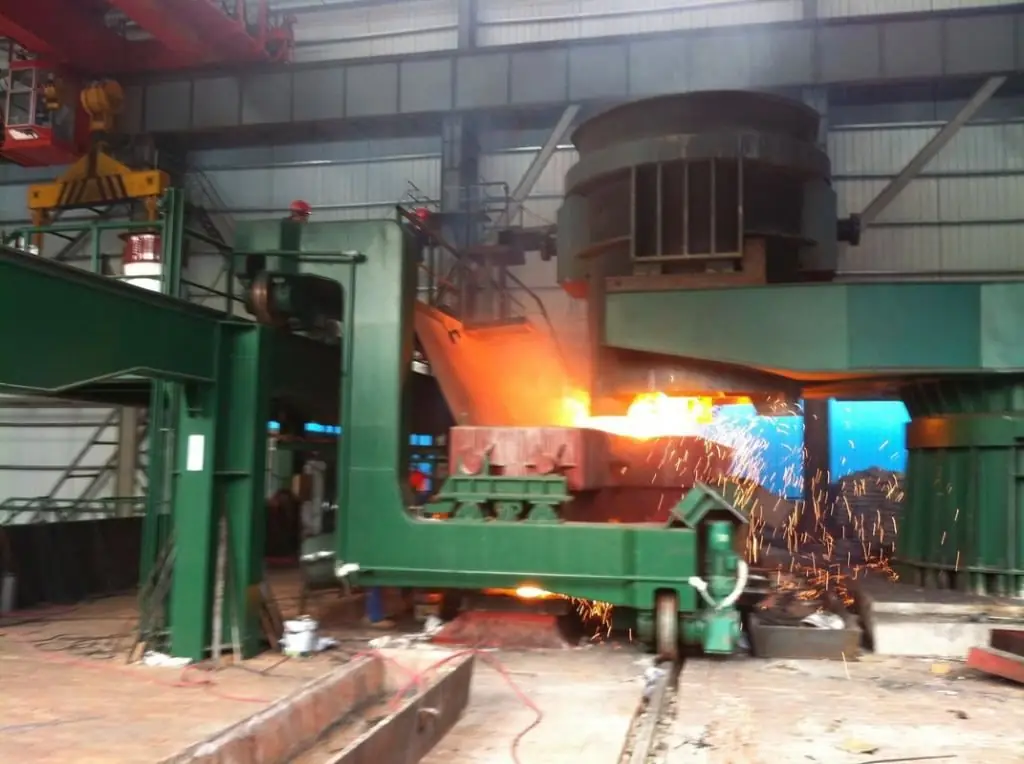
Zona pendinginan sekunder
Pada bagian ini, pendinginan ingot yang paling intensif dan langsung dilakukan dengan bantuan air yang berasal dari semprotan. Ada sistem khusus idle, bukan power roller. Rotasinya mencegah ingot dari tekukan atau bengkok. Karena pendinginan yang intens di zona ini, dinding ingot akan bertambah tebal dengan cepat, dan kristalisasi akan menyebar secara mendalam. Kecepatan penarikan ingot dan derajat pendinginannya harus dipilih sedemikian rupa sehingga pada saat ingot memasuki gulungan penarik, ingot sudah benar-benar padat.
Apa manfaat casting terus menerus
Karena metode pengecoran baja ini telah menggantikan metode penuangan ke dalam cetakan, ada baiknya membandingkan dengan metode ini. Secara umum, ada baiknya menyoroti keuntungan berikut: produktivitas yang lebih besar, pengurangan biaya dan pengurangan intensitas tenaga kerja dari proses tersebut. Karena pembentukan ingot yang konstan, rongga susut dipindahkan ke ekor, berbeda dengan cetakan ingot, di mana setiap batang memiliki rongganya sendiri. Karena itu, persentase hasil logam yang sesuai meningkat secara signifikan. UNRS memungkinkan Anda untuk mendapatkanbenda kerja dengan berbagai bentuk, dari persegi kecil 40x40 mm hingga persegi panjang 250x1000 mm. Penggunaan mesin pengecoran kontinu memungkinkan untuk sepenuhnya meninggalkan pabrik swaging. Ini secara signifikan mengurangi biaya proses produksi, dan karenanya harga di pasar. Selain itu, proses pengolahan metalurgi telah disederhanakan.
Kekurangan
Meskipun kemungkinan mekanisasi dan otomatisasi proses yang tinggi, persentase ingot yang baik dan keuntungan lain yang dijelaskan di atas, persentase tinggi yang tinggi, metode ini juga memiliki beberapa sisi negatif. Kerugian dari baja pengecoran kontinyu adalah sebagai berikut.
Pertama, tidak ada kemungkinan untuk menghasilkan ingot dengan konfigurasi yang rumit. Kedua, kisaran ingot dan blanko cukup terbatas. Cukup sulit untuk mengubah mesin untuk menuangkan bahan baku dari merek yang berbeda, yang dapat meningkatkan biaya akhir produk dari merek yang berbeda jika diproduksi di pabrik yang sama. Beberapa grade baja, misalnya, yang mendidih, tidak dapat dibuat menggunakan metode ini sama sekali.
Kerugian terakhir dari metode pengecoran baja kontinyu sangat signifikan. Ini adalah kemungkinan kegagalan peralatan. Kegagalan UNRS akan menyebabkan kerugian besar dalam kinerja. Semakin lama waktu perbaikan, semakin banyak kerugian yang akan bertambah.
Direkomendasikan:
Toko Rokok: persiapan dokumen yang diperlukan, menyusun rencana bisnis, pemilihan peralatan yang diperlukan, tujuan dan tahap pengembangan
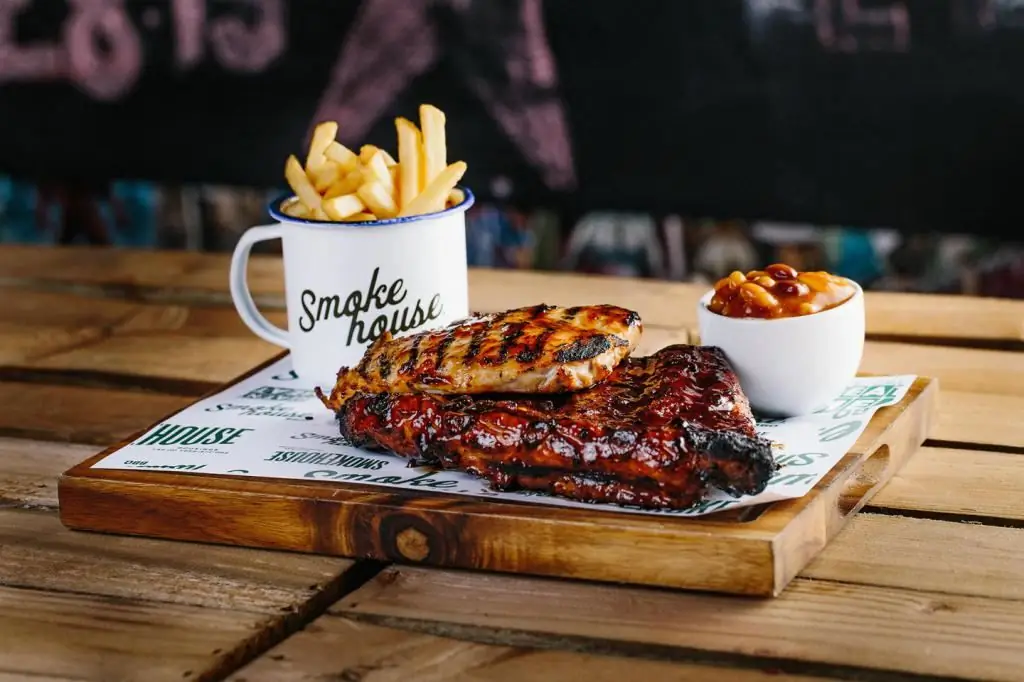
Artikel ini membahas bisnis seperti toko rokok. Pelajari cara memulai bisnis dan dari mana harus memulai. Tentang bagaimana memilih peralatan dan bagaimana seharusnya. Tentang apa yang perlu Anda perhatikan saat memilih pemasok, dan tentang proses pembuatan produk asap
Letterpress adalah Teknologi pencetakan letterpress, tahap perkembangan modern, peralatan yang diperlukan, kelebihan dan kekurangan dari jenis pencetakan ini
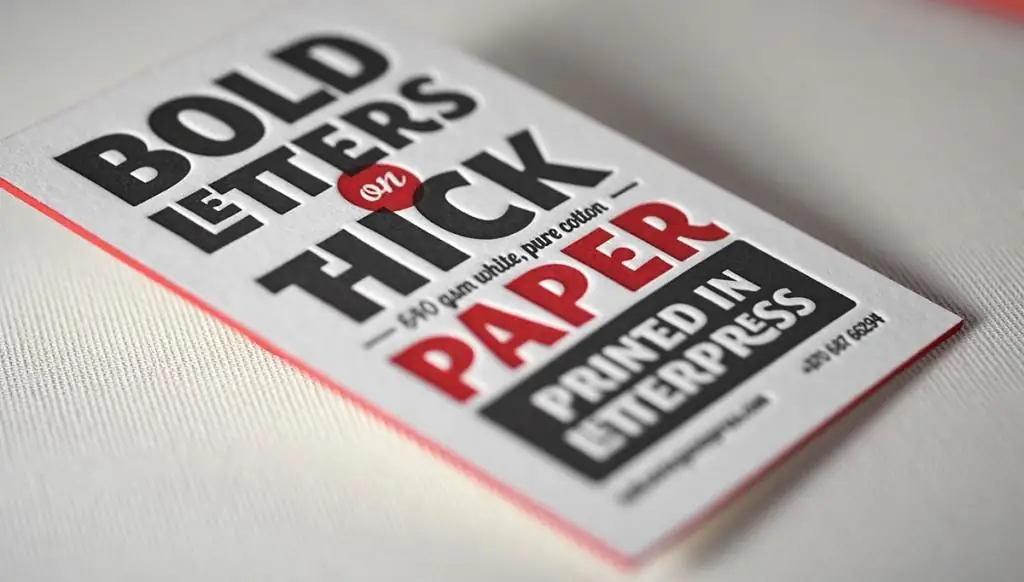
Letterpress adalah salah satu metode tipikal untuk menerapkan informasi menggunakan matriks relief. Elemen yang menonjol ditutup dengan cat dalam bentuk pasta, dan kemudian ditekan ke kertas. Dengan demikian, berbagai majalah massa, buku referensi, buku dan surat kabar direplikasi
Prinsip operasi diesel: fitur, kelebihan dan kekurangan
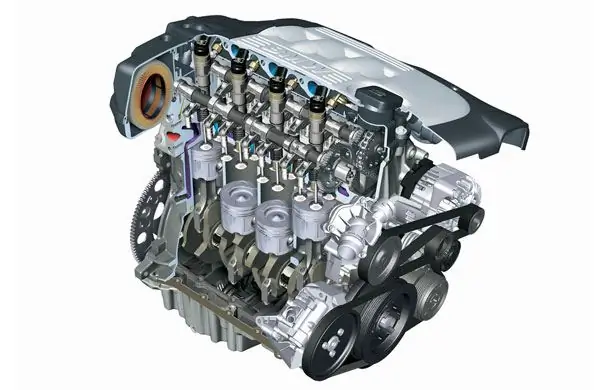
Mobil diesel di jalan kami bukanlah hal yang aneh. Di negara-negara Eropa Barat, mereka adalah mayoritas. Mesin diesel memiliki beberapa keunggulan dibandingkan mesin bensin. Tetapi pada saat yang sama, ada beberapa kelemahan. Apa motor ini, apa perangkat diesel dan prinsip operasinya? Pertimbangkan dalam artikel kami hari ini
Kapal selam diesel: sejarah pembuatan, proyek kapal, prinsip operasi, kelebihan, kekurangan, dan tahap pengembangan
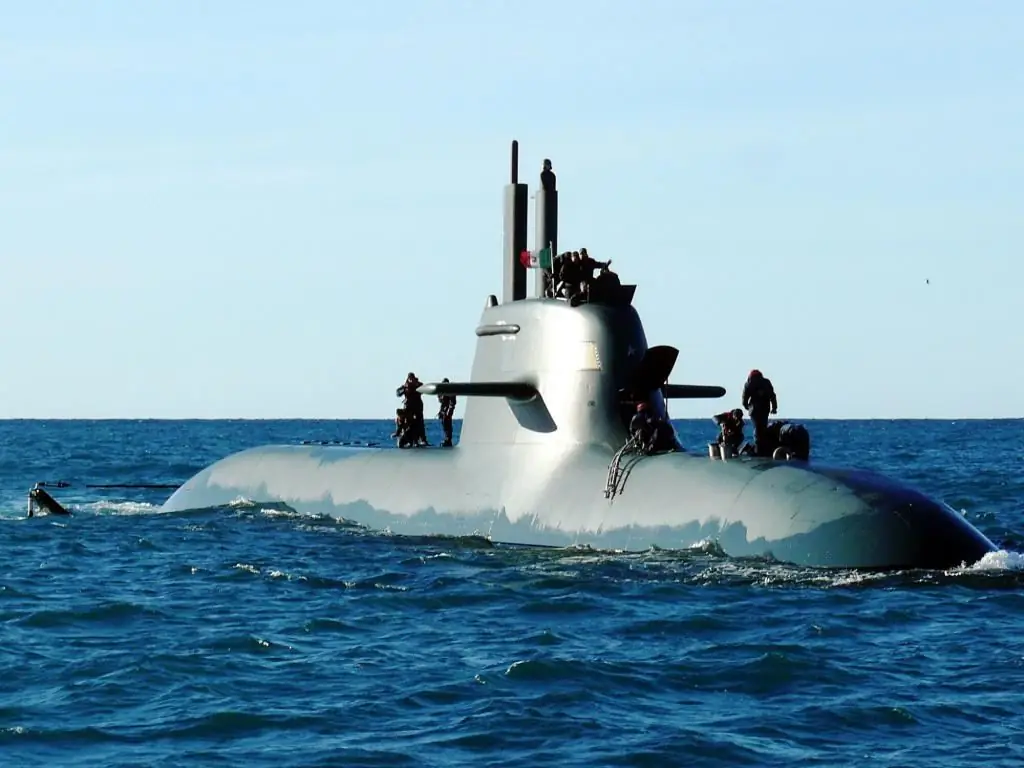
Ide membuat kapal selam yang bergerak di bawah air, sebenarnya prototipe kapal selam (selanjutnya disebut kapal selam), muncul jauh sebelum kemunculannya yang sebenarnya di abad ke-18. Tidak ada deskripsi pasti tentang kendaraan bawah air dalam banyak legenda, maupun dalam kejeniusan Renaisans Leonardo da Vinci
Pengecoran lilin yang hilang: teknologi, kelebihan dan kekurangan
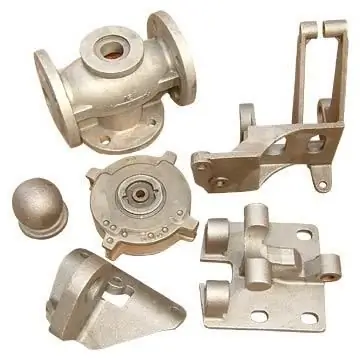
Penggunaan model investasi adalah metode produksi pengecoran yang cukup populer. Ini digunakan di mana perlu untuk mengamati dimensi secara akurat dan memastikan kualitas permukaan bagian yang tinggi. Beginilah cara pembuatan bilah turbin dan alat berkinerja tinggi, gigi palsu dan perhiasan, serta pahatan dengan konfigurasi yang rumit. Cetakan untuk pengecoran adalah satu bagian, model bahan dengan titik leleh rendah tidak dilepas selama pencetakan, tetapi dicairkan