2025 Pengarang: Howard Calhoun | [email protected]. Terakhir diubah: 2025-01-24 13:18
Produksi ramping adalah skema khusus manajemen perusahaan. Ide utamanya adalah untuk terus-menerus berusaha menghilangkan segala jenis biaya. Lean manufacturing merupakan konsep yang melibatkan keterlibatan setiap karyawan dalam prosedur optimasi. Skema semacam itu ditujukan untuk orientasi maksimal kepada konsumen. Mari kita lihat lebih dekat apa itu sistem lean manufacturing.
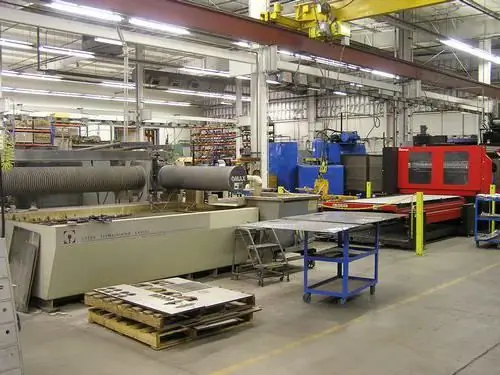
Riwayat kejadian
Pengenalan lean manufacturing ke dalam industri terjadi pada 1950-an di Toyota Corporation. Pencipta skema kontrol seperti itu adalah Taiichi Ohno. Kontribusi besar untuk pengembangan lebih lanjut dari teori dan praktik dibuat oleh rekannya Shigeo Shingo, yang, antara lain, menciptakan metode untuk perubahan cepat. Selanjutnya, spesialis Amerika menyelidiki sistem dan mengonsepnya dengan nama lean manufacturing (lean production) - "lean production". Pada awalnya, konsep ini diterapkan terutama di industri otomotif. Setelah beberapa saat, skema itu disesuaikan dengan prosesnyaproduksi. Selanjutnya, alat lean manufacturing mulai digunakan dalam perawatan kesehatan, utilitas, jasa, perdagangan, militer, pemerintah, dan industri lainnya.
Sorotan
Produksi ramping di perusahaan melibatkan analisis nilai produk yang diproduksi untuk konsumen akhir, pada setiap tahap pembuatan. Tujuan utama dari konsep ini adalah pembentukan proses eliminasi biaya yang berkelanjutan. Dengan kata lain, lean manufacturing adalah penghapusan aktivitas apa pun yang menghabiskan sumber daya tetapi tidak menciptakan nilai apa pun bagi pengguna akhir. Misalnya, dia tidak membutuhkan produk jadi atau komponennya dalam persediaan. Di bawah sistem tradisional, semua biaya yang terkait dengan pernikahan, pengerjaan ulang, penyimpanan, dan biaya tidak langsung lainnya dibebankan kepada konsumen. Lean manufacturing adalah skema di mana semua aktivitas perusahaan dibagi menjadi proses dan operasi yang menambah dan tidak menambah nilai pada produk. Oleh karena itu, tugas utama adalah pengurangan sistematis dari yang terakhir.
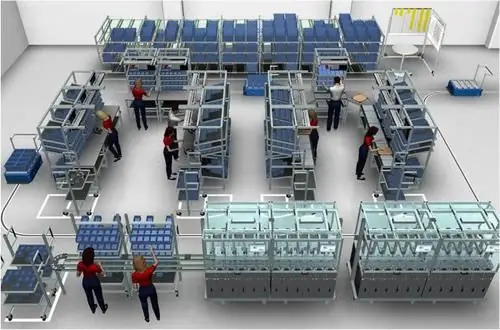
Lean waste
Sebagai sinonim untuk biaya, istilah muda terkadang digunakan. Konsep ini berarti berbagai pengeluaran, sampah, pemborosan dan sebagainya. Taiichi Ohno mengidentifikasi tujuh jenis biaya. Kerugian dihasilkan karena:
- tunggu;
- kelebihan produksi;
- pengiriman;
- langkah pemrosesan ekstra;
- gerakan yang tidak perlu;
- melepaskan barang cacat;
- persediaan berlebih.
Jenis kerugian utama yang dianggap Taiichi Ohno adalah kelebihan produksi. Ini adalah faktor yang menyebabkan timbulnya biaya lain. Item lain telah ditambahkan ke daftar di atas. Jeffrey Liker, seorang peneliti tentang pengalaman Toyota, menyebut potensi karyawan yang belum direalisasi sebagai pemborosan. Sumber biayanya adalah kelebihan kapasitas, pegawai saat melakukan aktivitas dengan intensitas yang meningkat, serta tidak meratanya pelaksanaan operasi (misalnya jadwal yang terganggu karena fluktuasi permintaan).
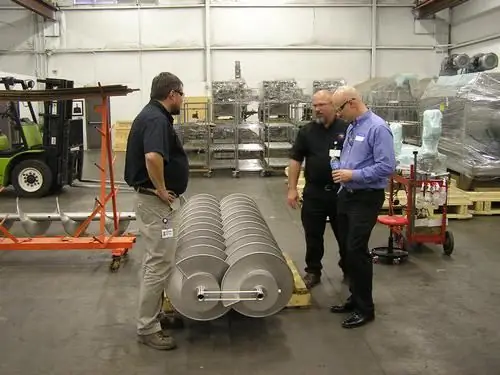
Prinsip
Lean manufacturing disajikan sebagai proses yang dibagi menjadi lima tahap:
- Menentukan nilai produk tertentu.
- Tetapkan aliran nilai produk ini.
- Memastikan aliran berkelanjutan.
- Memungkinkan konsumen untuk menarik produk.
- Berjuang untuk keunggulan.
Di antara prinsip-prinsip lain yang menjadi dasar lean manufacturing, kita harus menyoroti:
- Mencapai kualitas yang sangat baik - pandangan pertama, nol cacat, mengidentifikasi dan menyelesaikan masalah pada tahap awal.
- Menciptakan hubungan jangka panjang dengan konsumen melalui berbagi informasi, biaya dan risiko.
- Fleksibilitas.
Sistem produksi,digunakan di Toyota didasarkan pada dua prinsip utama: otonomi dan "tepat waktu". Yang terakhir berarti bahwa semua elemen yang diperlukan untuk perakitan tiba di jalur tepat pada saat dibutuhkan, secara ketat dalam jumlah yang ditentukan untuk proses tertentu untuk mengurangi stok.
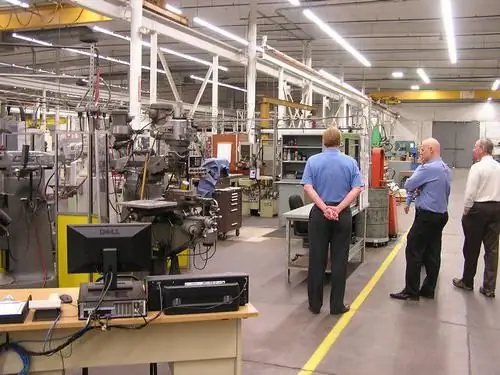
Elemen komposisi
Dalam kerangka konsep yang sedang dipertimbangkan, berbagai komponen dibedakan - metode produksi ramping. Beberapa dari mereka mungkin sendiri bertindak sebagai skema kontrol. Unsur-unsur utama termasuk yang berikut:
- Aliran item tunggal.
- Perawatan peralatan umum.
- 5S sistem.
- Kaizen.
- Pergantian cepat.
- Pencegahan kesalahan.
Opsi Industri
Lean he alth adalah sebuah konsep untuk mengurangi waktu yang dihabiskan oleh staf medis yang tidak terkait langsung dengan membantu orang. Logistik ramping adalah skema tarik yang menyatukan semua pemasok yang terlibat dalam aliran nilai. Dalam sistem ini, ada pengisian sebagian cadangan dalam volume kecil. Indikator utama dalam skema ini adalah total biaya logistik. Alat lean manufacturing digunakan oleh Kantor Pos Denmark. Sebagai bagian dari konsep, dilakukan standarisasi besar-besaran terhadap layanan yang ditawarkan. Tujuan dari acara ini adalah untuk meningkatkan produktivitas, mempercepat transfer. "Kartu pembentukan nilai sebaris" diperkenalkanuntuk mengontrol dan mengidentifikasi layanan. Juga, sistem motivasi bagi karyawan departemen dikembangkan dan kemudian diimplementasikan. Dalam konstruksi, strategi khusus telah dibentuk, difokuskan pada peningkatan efisiensi proses konstruksi di semua tahap. Prinsip lean manufacturing telah disesuaikan dengan pengembangan perangkat lunak. Elemen skema yang dipertimbangkan juga digunakan dalam administrasi kota dan negara bagian.
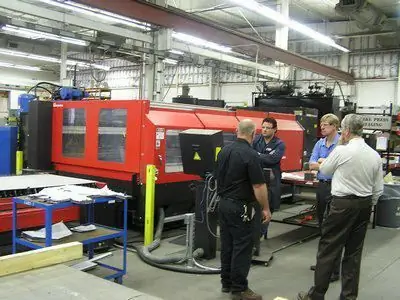
Kaizen
Gagasan ini dirumuskan pada tahun 1950 oleh Dr. Deming. Pengenalan prinsip ini telah membawa keuntungan besar bagi perusahaan Jepang. Untuk ini, spesialis dianugerahi medali oleh kaisar. Setelah beberapa saat, Persatuan Sains dan Teknologi Jepang mengumumkan hadiah untuk mereka. Deming untuk kualitas barang manufaktur.
Manfaat Filosofi Kaizen
Manfaat sistem ini telah dievaluasi di setiap sektor industri, di mana kondisi telah diciptakan untuk memastikan efisiensi dan produktivitas tertinggi. Kaizen dianggap sebagai filosofi Jepang. Ini terdiri dalam mempromosikan perubahan berkelanjutan. Aliran pemikiran kaizen menegaskan bahwa perubahan konstan adalah satu-satunya jalan menuju kemajuan. Penekanan utama dari sistem ini adalah pada peningkatan produktivitas dengan menghilangkan kerja keras dan tidak perlu. Definisi itu sendiri dibuat dengan menggabungkan dua kata: "kai" - "perubahan" ("transformasi"), dan "zen" - "ke arah yang lebih baik." Keunggulan sistem tersebut cukup jelas mencerminkan keberhasilan ekonomi Jepang. Hal ini diakui tidak hanya oleh orang Jepang sendiri, tetapi juga oleh para ahlidamai.
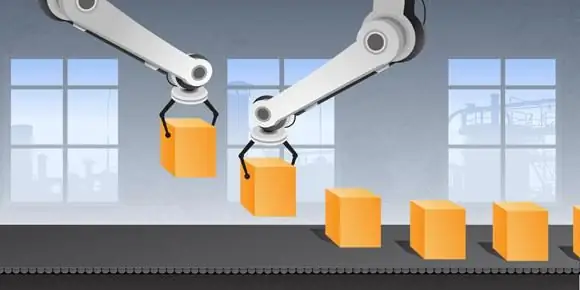
Tujuan Konsep Kaizen
Ada lima arah utama pengembangan produksi yang dilakukan. Ini termasuk:
- Pengurangan sampah.
- Pemecahan masalah segera.
- Penggunaan yang optimal.
- Kerja Tim.
- Kualitas terbaik.
Harus dikatakan bahwa sebagian besar prinsip didasarkan pada akal sehat. Komponen utama dari sistem tersebut adalah peningkatan kualitas barang, melibatkan setiap karyawan dalam proses, kesiapan untuk interaksi dan perubahan. Semua kegiatan ini tidak memerlukan perhitungan matematis yang rumit atau pencarian pendekatan ilmiah.
Pengurangan sampah
Prinsip-prinsip filosofi kaizen ditujukan untuk mengurangi kerugian secara signifikan pada setiap tahap (operasi, proses). Salah satu keuntungan utama skema ini adalah mencakup setiap karyawan. Ini, pada gilirannya, melibatkan pengembangan dan implementasi selanjutnya dari proposal untuk perbaikan di setiap tingkat manajemen. Pekerjaan seperti itu berkontribusi untuk meminimalkan hilangnya sumber daya.
Pemecahan masalah segera
Setiap karyawan, sesuai dengan konsep kaizen, harus mengatasi masalah. Perilaku ini berkontribusi pada penyelesaian masalah yang cepat. Dengan pemecahan masalah segera, waktu tunggu tidak bertambah. Penyelesaian masalah dengan segera memungkinkan Anda mengarahkan aktivitas ke arah yang efektif.
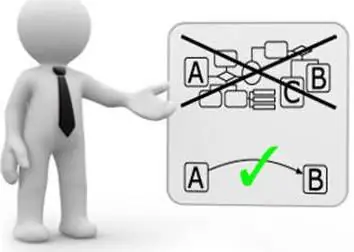
Penggunaan optimal
Sumber daya dilepaskan ketika masalah diselesaikan dengan cepat. Mereka dapat digunakan untuk meningkatkan dan mencapai tujuan lain. Bersama-sama, langkah-langkah ini memungkinkan untuk membangun proses produksi yang efisien secara berkelanjutan.
Kerja Sama
Melibatkan semua karyawan dalam menyelesaikan masalah memungkinkan Anda menemukan jalan keluar lebih cepat. Berhasil mengatasi kesulitan memperkuat semangat dan harga diri karyawan perusahaan. Kerja tim menghilangkan situasi konflik, mendorong pembentukan hubungan saling percaya antara karyawan yang lebih tinggi dan yang lebih rendah.
Kualitas terbaik
Pemecahan masalah yang cepat dan efisien berkontribusi pada kerja tim dan penciptaan sumber daya dalam jumlah besar. Ini, pada gilirannya, akan meningkatkan kualitas produk. Semua ini akan memungkinkan perusahaan untuk mencapai tingkat kapasitas yang baru.
Direkomendasikan:
Produksi oli motor: karakteristik, teknologi, dan proses manufaktur
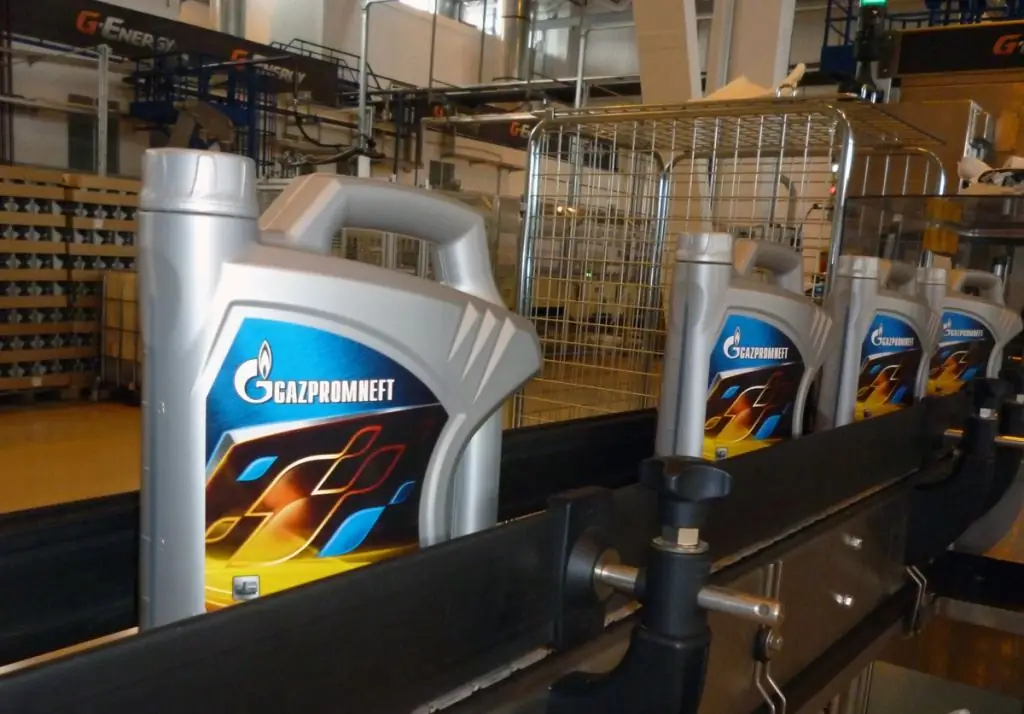
Produksi oli motor, seperti yang lainnya, tidak lengkap tanpa bahan mentah - bahan dari mana produk akhir diperoleh. Minyak mineral terbuat dari minyak bumi. Namun sebelum sampai ke pabrik pelumas, harus melalui serangkaian pembersihan di kilang minyak
Produksi modern. Struktur produksi modern. Masalah produksi modern

Industri yang berkembang dan tingkat ekonomi negara yang tinggi merupakan faktor kunci yang mempengaruhi kekayaan dan kesejahteraan rakyatnya. Negara seperti itu memiliki peluang dan potensi ekonomi yang besar. Komponen penting dari perekonomian banyak negara adalah produksi
Rencana bisnis produksi styrofoam: langkah-langkah pembukaan, teknologi manufaktur, perhitungan pendapatan dan pengeluaran
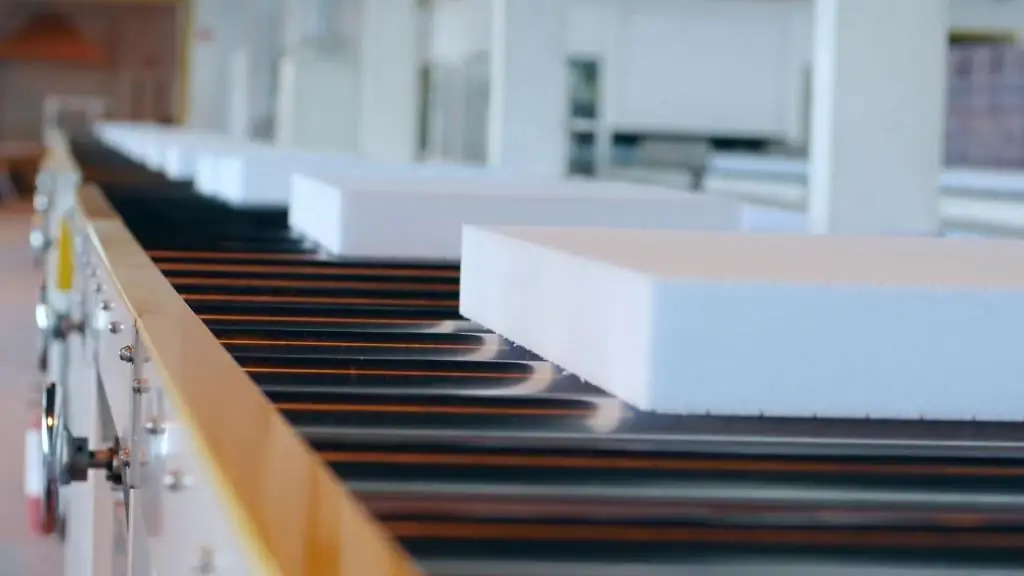
Polyfoam dapat dikaitkan dengan salah satu bahan bangunan yang paling banyak digunakan. Permintaannya cukup tinggi, seiring dengan perkembangan pasar penjualan, yang dengan pendekatan pemasaran yang kompeten, dapat memberikan keuntungan yang stabil untuk jangka waktu yang lama. Pada artikel ini, kami akan mempertimbangkan secara rinci rencana bisnis untuk produksi plastik busa
Produksi gas. Metode produksi gas. Produksi gas di Rusia
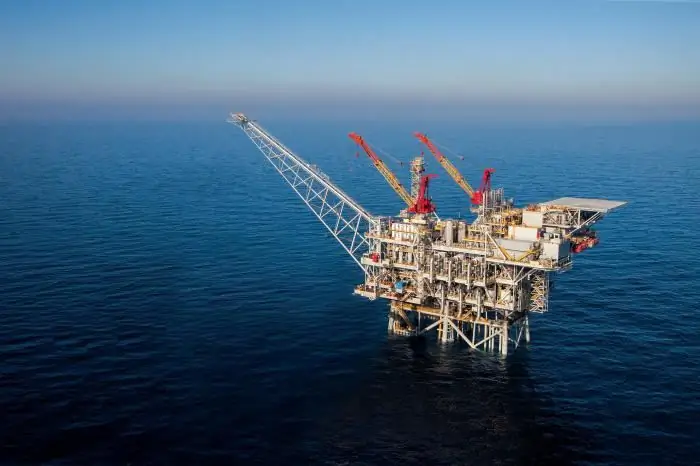
Gas alam terbentuk dengan mencampurkan berbagai gas di kerak bumi. Dalam kebanyakan kasus, kedalaman kejadian berkisar dari beberapa ratus meter hingga beberapa kilometer. Perlu dicatat bahwa gas dapat terbentuk pada suhu dan tekanan tinggi. Dalam hal ini, tidak ada akses oksigen ke tempat itu. Sampai saat ini, produksi gas telah diimplementasikan dalam beberapa cara, yang masing-masing akan kami bahas dalam artikel ini. Tapi mari kita bicarakan semuanya secara berurutan
Produksi karpet: teknologi dan fitur manufaktur
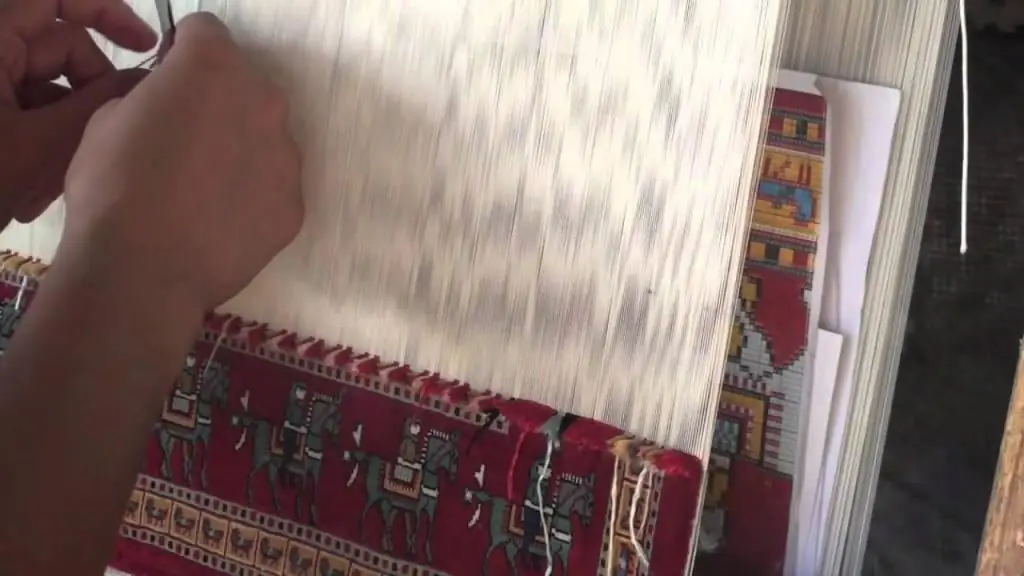
Setiap produksi karpet dimulai dengan pemilihan bahan baku. Dan jika sebelumnya pilihan bahan terbatas pada wol dan sutra, hari ini Anda dapat menemukan kain tenun dari serat alami dan rekan sintetisnya